Masonry involves the construction of natural building stone, bricks, concrete block, adobe, or glass blocks bonded together with mortar. These units may be load-bearing or non-load bearing, and steel reinforcement is often added for strength.
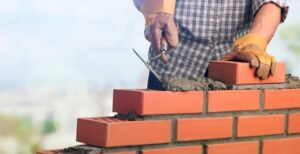
Understanding this construction method allows developers to optimize resources and place projects on a path toward success. Contact Charleston Masonry Masters for professional help.
First impressions are everything, and few exterior enhancements speak more to your style than a charming brick path or a sturdy retaining wall. Whether you’re looking for a way to welcome guests or make it easier for family members to navigate the yard, masonry is the perfect solution.
In addition to its classic aesthetic, masonry is durable and low maintenance. With periodic cleaning, repointing, and sealing, these hardscaping elements will last for years to come. Plus, they require far less work than wood structures, which need frequent staining and sealing.
Masonry adds a touch of elegance to your home’s exterior, and it can even boost its value. In fact, many homeowners find that their investment in a masonry project pays off when they decide to sell. This is because buyers associate well-maintained masonry with a higher level of overall construction and attention to detail.
With so many benefits, it’s no wonder that masonry is one of the most popular landscaping choices for homes. From driveways and patios to garden features and more, this versatile building material offers limitless opportunities for improving your curb appeal.
When designing your masonry layout, experiment with different laying patterns to create visual interest and uniqueness. For example, try herringbone, basketweave, or running bond to add texture and dimension. Also, pay close attention to scale. Using larger stones can make an impressive statement, while smaller ones will create a more intimate feel.
Color is also a crucial element in masonry design, as it can elevate the overall appearance of your property. For example, earthy tones like warm browns and reds enhance classic brick and stone appearances while adding a sense of rustic charm. Meanwhile, sleek grays and blacks can add a contemporary edge to modern homes.
When you’re ready to explore your options for enhancing your curb appeal with masonry, talk to a trusted professional. In addition to checking references and confirming licensing and certifications, you should also ask about insurance coverage, which should include both general liability and workers’ compensation. This will protect you in case of any damages or injuries caused during the project.
Structural Strength
Masonry is one of the oldest and most respected construction techniques in human history, and it continues to provide a safe, durable and beautiful building material. The strength of masonry is due to the fact that each unit is composed of solid stone, brick or concrete block bound together with mortar. Engineers recognize the importance of understanding how geometric forms affect structural integrity when designing high-rise buildings and bridges, as well as ensuring overall stability for structures in use for generations to come.
The beauty of a masonry structure is determined by the quality of the materials used and the skill of the mason. Masons can create a rustic or elegant look for walls, fireplaces and more by choosing different stones to fit together purposefully. A skilled mason can even construct arches and other structures with a unique, distinctive appearance that adds to the aesthetic value of any building.
Structural strength of masonry is also influenced by the geometry of the individual units and the way they are assembled. For example, a wall constructed of single-wythe brick in a serpentine pattern is stronger than a straight wall of the same size and material. The friction between the blocks helps to provide some of this strength. In addition, many masonry structures are reinforced with steel rebar, which increases the strength and durability of the finished structure.
Unlike wood, masonry is not susceptible to rot or insect damage. This can save building owners money on maintenance and repairs over time. Masonry is also non-combustible, which improves safety for the occupants of a home or business and may help prevent fires. Masonry walls and structures are also resistant to projectiles during natural disasters such as hurricanes or tornadoes, which makes them a good choice for areas in danger of being hit by debris.
In addition to its aesthetic and functional benefits, masonry is an excellent choice for remodeling existing homes and businesses. It is often possible to upgrade existing buildings to meet increased loads without the need for extensive and costly reconstruction. This is particularly important in older structures that are at risk of collapse. Structural strengthening can restore the original integrity of a building, reducing the risk of a collapsed roof or other structural failures.
Energy Efficiency
Masonry is not only durable and stylish, but it’s also energy efficient. This is largely due to its natural thermal mass properties that absorb and slowly release heat. This helps to stabilize indoor temperatures and reduce the need for constant air conditioning. Additionally, brick walls can act as a sound barrier to keep a home quieter and more comfortable.
Energy Efficiency
Load-bearing concrete masonry is a great choice for the inner walls of a building, providing excellent insulation to reduce heat transfer between the inside and outside of a structure. It is often used in conjunction with cavity walls made of fiberglass or polystyrene. When combined with appropriate insulation, the interior walls of a masonry building can achieve an R-Value up to 20 when properly installed.
This makes it a highly energy-efficient solution that can withstand Toronto’s harsh weather conditions without requiring extensive HVAC system upgrades or maintenance. Masonry also provides a tight seal that prevents outside moisture from damaging or contaminating the interior walls, resulting in lower water and energy bills.
Another benefit of masonry is its ability to absorb and retain sunlight, which naturally heats the building during the day. At night, the bricks help to cool the building by releasing stored heat. It’s this quality that gives masonry its energy-efficiency benefits, and it’s something that is increasingly being valued in the modern home.
In addition to the thermal mass benefits, concrete masonry also offers exceptional structural performance and durability. Concrete blocks, commonly known as CMUs, are available in a variety of sizes and shapes, allowing builders to choose a wall system that best fits their project’s needs. These blocks can be incorporated into load-bearing or non-load bearing walls, and they can provide either an open or closed cavity.
When compared to buildings with a wood frame, masonry walls can save up to 33% in energy consumption by eliminating the need for constant air conditioning. In addition to these savings, the use of masonry can significantly reduce greenhouse gas emissions and other environmental pollutants. This can be especially beneficial in areas that have implemented off-peak electricity pricing programs, where energy usage is cheaper at times of peak demand.
Environmental Sustainability
Masonry provides a broad solution for sustainability and green design, including a holistic approach to energy efficiency, resilience, waste reduction, adaptive reuse, and occupant well-being. This holistic approach considers the entire life cycle of masonry, from raw materials to construction and demolition, and addresses finite natural resources, recyclability, and a focus on environmental impact.
Buildings consume 28% of the world’s energy and produce 21% of global greenhouse gases. Both the energy used to heat, cool and ventilate buildings and the emissions generated by the production of construction materials account for this footprint. Brick and other masonry materials, when made using eco-friendly practices, reduce this burden.
The thermal mass properties of masonry regulate indoor temperatures more efficiently, lowering heating and cooling costs, and the dependency on fossil fuels for energy. Masonry can also be constructed with recycled brick, sourced locally to diminish transportation and quarrying emissions. Additionally, concrete masonry units can be made with reduced cement content or even with industrial byproducts to reduce emissions even further.
Non-combustible masonry construction contributes to the longevity of buildings, reducing maintenance needs and material waste. Additionally, buildings constructed with eco-friendly masonry techniques can earn certifications for sustainability programs like LEED, further boosting their marketability and resale value.
While products such as plastics and many synthetic building materials claim to be maintenance-free, they do not serve as stepping stones toward a sustainable future. Conversely, durable masonry construction can help communities meet their sustainability goals by protecting their residents and the environment against the impacts of uncontrollable wildfires; hurricanes, tornadoes, or other high wind events; ice or snowstorms; and earthquakes.
The environmental footprint of masonry construction depends on the choice of concrete, cement replacement, and aggregate. A high quality, dense, low-porosity aggregate with minimal voids is key to a long service life and lower environmental impact. Additionally, lightweight CMUs with a lower percentage of crystalline silica, such as those made with expanded shale, clay and slate (ESCS), are less demanding on the mason workforce due to fewer health concerns related to respiration and exposure to hazardous dust. These sustainable practices, along with the inherent durability of masonry, contribute to a more environmentally responsible future for both mason contractors and their customers.